What are the two most common types of polyurethane and which is best for me?
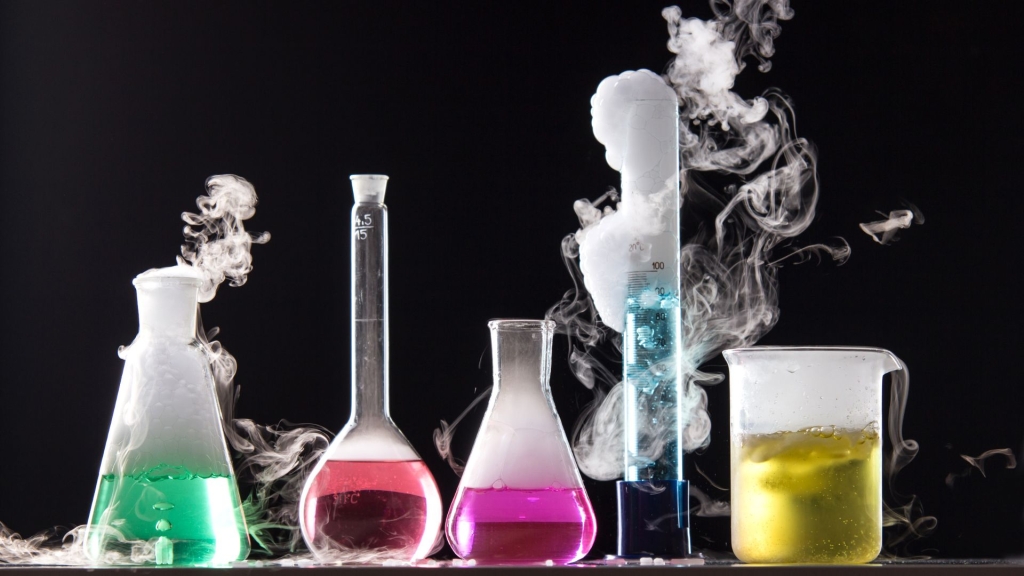
Polyurethane (PU) is widely used as a versatile and durable coating and finish. Polyurethane is the result of a chemical reaction, which can be composed of different resins, the two most common types being alkyd and acrylic.
In this blog, we’ll explore the key differences between alkyd and acrylic PUs, so you can decide which is best suited for your next project.
What is the difference between alkyd and acrylic PUs?
Alkyd PUs are made using an alkyd resin base, whereas acrylic PUs are formulated by using acrylic resin base. Two very different styles of coating that both use isocyanate hardeners to create the chemical reaction that forms polyurethane.
The most noticeable differences between the two are:
Health and safety
Alkyd PUs: Contain high levels of aromatic isocyanates, which can be harmful to users and raise health and safety concerns. Alkyds need to be handled correctly, with proper safety measures in place.
Acrylic PUs: Are safer and do not use aromatic isocyanates to trigger the reaction.
Yellowing
Alkyd PUs: Are more prone to yellowing over time, especially when exposed to UV light, which can affect the appearance of the finish.
Acrylic PUs: Do not yellow, making them a better choice for maintaining the original colour and appearance of the coated surface, especially when using pale colours or coating pale substrates.
Durability
Both styles of product can be equally durable depending on the intentions of the manufacturer with regard to the end use of the product.
Drying time
Alkyd PUs: Tend to have a shorter drying time for a given solids level, although this is not a hard and fast rule.
Acrylic PUs: Acrylic polyurethanes tend to dry slower for a given solids level.
For example, the opposite may appear true in many cases because the general clear multicoat acrylic PU will dry faster than the average alkyd equivalent due to to its lower solids level. A high solids acrylic base coat will be much slower drying than it’s alkyd equivalent.
Odour
Alkyd PUs: Have a sweeter solvent-based odour, which can be quite noticeable during application.
Acrylic PUs: Have a more fruity odour.
In either case the safety of a product is not linked to its level of safety. Very often the most toxic solvents can be very subtle indeed.
The pros and cons of Alkyd
Alkyd PUs are still very popular, especially within the Italian market, where they are typically produced, for various reasons:
Pros of alkyd
Very high build product
- Clarity is marginally better than acrylic
However, there are some cons to be considered:
Cons of alkyd
Contains high levels of aromatic isocyanates, which can be toxic to users if not handled properly
- Alkyds are usually 2:1, or 1:1 mix so the level of isocyanates is increased further
- Causes discolouration of the wood and yellowing over time
Although most of the PU coatings we stock are acrylic, we do recommend the Hesse product, Optibase, for a reliable finish.
The pros and cons of Acrylic
At Redwood, we stock a wide range of acrylic PUs to suit your needs. You will find, in our Hesse range, all the PU products are acrylic, except the DG4750 and DG4720.
Why we rate acrylic PUs:
Pros of acrylic
Safer, with no aromatic isocyanates
- Smaller mix ratios, better for both applicator and the environment (less harmful emissions)
- No discolouration of wood
- Has a longer pot life once mixed with hardener (up to 3 days!)
- Less hardener is required
It is important to consider what is right for your project:
Cons of acrylic
Lower solid content level than alkyd. It may take more coats to achieve the same coverage as alkyd.
If you would like some assistance in choosing the right solution, our knowledgeable team is always happy to help.
For a PU solution that meets your project’s requirements. Contact us on 023 9223 3310 or email sales@redwood-uk.com